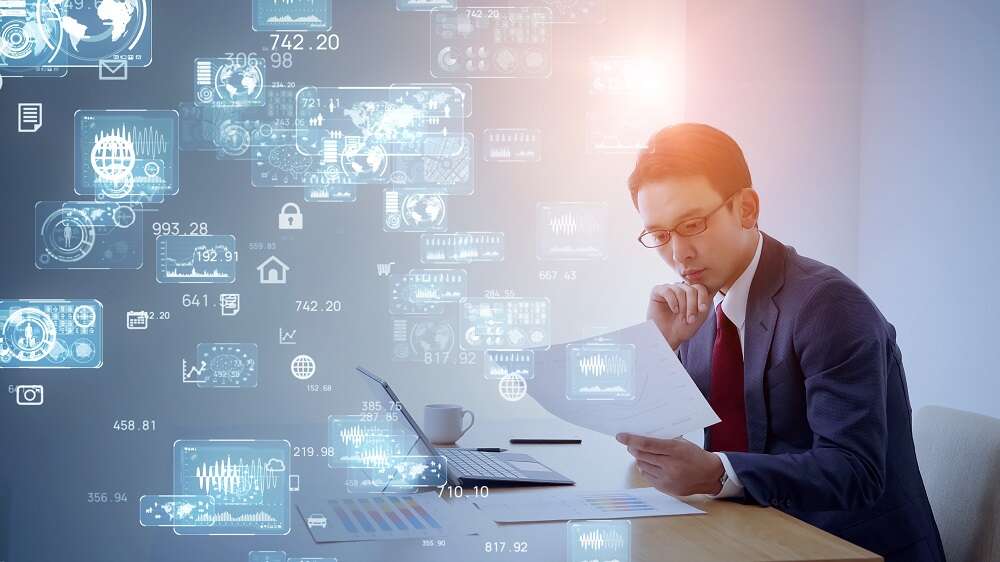
By Dan Johnson, Director Product Marketing, Kofax
The toilet paper shortage of 2020 is–thankfully–long gone.Still, global supply chains continue to struggle as the pandemic lingers and other unexpected events unfold. Another surge of Covid cases in China and the global impacts from the crisis in Ukraine are two of the most recent issues squashing the hope that supply chain issues will get better this year.
Various products and raw materials from oil to computer chips remain in short supply, and ports are experiencing unprecedented logjams. Even when the goods on board are finally unloaded, there often aren’t enough trucks (or truck drivers) to deliver items to their final destinations.
To say transportation and logistics (T&L) operations are challenged is an understatement. Of course, the immediate shortages and backlog will eventually subside, but the past two years have proven another disruption will likely pop up in its place. T&L companies need to take a hard look at their processes and workflows to ensure they can survive the current supply chain disruption and all the ones sure to follow.
The solution lies in intelligent automation, which delivers cost savings, improvements in productivity and efficiency and better customer service. A combination of technologies like artificial intelligence (AI), optical character recognition (OCR) and robotic process automation (RPA)transform T&L companies into agile and resilient machines capable of successfully navigating the new normal of constant supply chain issues.
If you’re wondering exactly how it all works, keep reading for a closer look at the logistics of intelligent automation implementation among three leading T&L providers. You’ll quickly see how automation transported all three businesses to supply chain safety and ahead of the competition.
Informed Customers Are Loyal Customers
Let’s face it. No one likes to wait for anything these days. Customers expect to have orders delivered quickly. The pandemic has certainly forced many people to develop patience as many items and materials are on backorder, but clients don’t have tolerance for lack of communication. They want to know the status of their order–in real time–so they can adjust to delays as quickly as possible. Intelligent automation makes this possible, and Davies Turner is taking full advantage of it.
Davies Turner is an international freight forwarding company and logistics specialist, headquartered in the UK. They provide shipping and logistics for land, air and sea freight, in addition to warehouse management and distribution services. They had been relying on a manual approach when customers inquired about an order status. But given the volume of shipments and the breadth of operations, the manual system was resulting in poor customer service. The company manages 10,000 shipments a day for just one customer, so just imagine how hard it was to find updates manually.
Employees often had to go through several steps to receive an update, searching tracking systems and going to the carrier’s website. Sometimes they even had to call or email the carrier. The result? It typically took anywhere from 10 to 15 minutes just to give the customer a simple status update. The slow response was hurting clients, wasting their time, and preventing them from responding swiftly to delays in shipments. They risked losing customers if they couldn’t find a faster, more efficient way to retrieve and share this vital information.
Davies Turner used RPA and put software robots to work. The bots extract and integrate data from their internal logistics and warehouse management systems (WMS), external carrier tracking solutions, and third-party websites. Manual entry has been eliminated, improving data accuracy. Shipments are tracked in real time, and the information stored in all relevant systems is easily accessible. Employees have the information ready before a customer even asks for it.
Thanks to RPA, the customer experience has been transformed. An email goes out as soon as an order leaves the warehouse. The email includes a link that tracks the order in real time, so customers can check the status whenever they want. Davies Turner took RPA one step further and applied it to inventory tracking. Now, they can also automatically notify customers if a particular inventory line goes out of stock.
Customers have access to the information they need to plan for shipment delays and to avoid dreaded out-of-stock situations. As a result, clients can take a proactive approach to managing their own business.
RPA bots are also simple to build and deploy, making it easy to scale. In fact, even non-technical employees can have a bot up and running in less than a half hour. More than 520 RPA bots that are executing more than 7,500 times per day has enabled Davies Turner to grow their customer base without increasing headcount.
Saving Time and Money Is Always a Win
What company doesn’t want to improve productivity and save money? Many transportation and logistics companies, however, struggle in these areas when it comes to the integration of data. If you look at trucking companies as an example, they often use vehicle telematic and transportation management systems (TMS) for fleet management. Transferring data between these systems and other relevant applications is often done manually–wasting time and money (and often resulting in errors).
Ron Finemore Transport was struggling with data integration, but they leveraged RPA and intelligent automation to reduce costs and improve productivity. The company operates an extensive logistics network across Australia’s eastern seaboard, providing logistics services for grocery distribution, primary freight from manufacturers to retail distribution centers, manufactured goods, complex linehaul services, produce, bulk liquids, grain and animal feed. In an effort to improve customer service and provide real-time updates, the company outfitted its vehicles with telematics devices and deployed a new TMS. However, integration was more complex than expected. As a result, employees were manually entering data from the telematics system into the TMS. Needless to say, the process was slow, with the equivalent of six FTEs per day spending time on manual data entry.
Everything changed once RPA bots were put to work. Now, a bot imports the real-time location of each vehicle into a central data warehouse and matches the record to the corresponding route in the TMS. When a truck enters or leaves a geofenced location (such as a fueling station or freight terminal) the appropriate delivery status is automatically updated in the TMS.
Seamless integration has improved customer service with real-time updates, but it has also unlocked a host of back-office efficiencies. Manual data entry has been reduced from six FTEs down to just half of one FTE per day, delivering a 91 percent efficiency improvement.
In response to these benefits, Ron Finemore expanded automation to other business processes as well, including the collection of fuel prices. Whereas a team member used to spend 20 minutes per day gathering and inputting this data, an RPA bot gets it done in just three minutes. They also automated the order acceptance process for a large customer, improving its data quality score from 70 percent to more than 90 percent.
All in all, the company saw a six-month return on investment in automation, making it a significant cost-saver for the long term. In fact, the company estimates it has saved anywhere from $800,000 to $1 million in overhead since implementation.
Don’t Let Paper Slow Your Supply Chain Down
The only things worse than unanticipated supply chain disruptions is the all-too-common paper document bottleneck. The sheer volume of paper forms involved in the shipping process is enough to bog down even the best T&L provider.
Custom forms differ in format between countries. Proof of delivery (POD) documents pile up quickly. T&L providers must be able to accurately identify and process each form accurately. Oftentimes, POD is captured through digital scanners, but scanners aren’t available at every location. Additionally, some shipments require a manual signature. In this scenario, POD documents have to be manually scanned, which often results in inaccuracies.
Fortunately, the paper bottleneck is no match for intelligent automation. DB Schenker, a globally integrated logistics services provider, was already moving away from paper. Customers had access to an electronic data exchange of all pertinent shipping information, delivery times, and performance indicators. Shipments were tracked with an online tracking system, and bar code labels made it possible to monitor individual items within a shipment. The ePOD delivery notification, however, is one of the most important pieces of information for each shipment, as it confirms whether the goods have arrived at their destination on time and without complications.
Most of the company’s drivers had delivery scanners, but there were some instances where the company wasn’t able to implement them. There were also direct deliveries that had to be handled on paper and digitised further down the process. While this was not a large percentage of deliveries, it was enough to add up to 600,000 pages of paper a year. Enough to cause a bottleneck? Absolutely. So they turned to intelligent automation.
In addition to being cost-effective and easy to manage, the solution had to be able to scan extremely well. This was a challenge, as delivery slips are often crumpled up, torn or even covered in grease. The system also needed to have interfaces for all important applications and support all standard scanners.
A combination of AI, RPA and OCR proved to the perfect blend of automation technologies. Embedded AI technologies like natural language processing combined with optical character recognition to create digital images of forms and extract the required information–at a high level of quality. RPA then delivers the data to the required systems and applications50 times faster than a human could, improving the lead time for updates by 80 percent. Faster access to this information helps customers manage their supply chains as conditions change.
The company also used automation to help with the massive increase in paper documents resulting from Brexit. The team used a sampling of documents to train the system via machine learning. As a result, DB Schenker was able to ease the Brexit burden on its customers.
The system can connect to all standard scanners and multi-function devices easily and paid for itself in a few weeks. In fact, it was less expensive than purchasing delivery scanners for all locations. The digitisation of paper-based delivery processes saved money and improved productivity.
Supply chain disruptions may be unpredictable, but T&L providers can still navigate to safety while keeping their customers informed, reducing costs and improving efficiencies. With intelligent automation, agility and resiliency will never be in short supply.