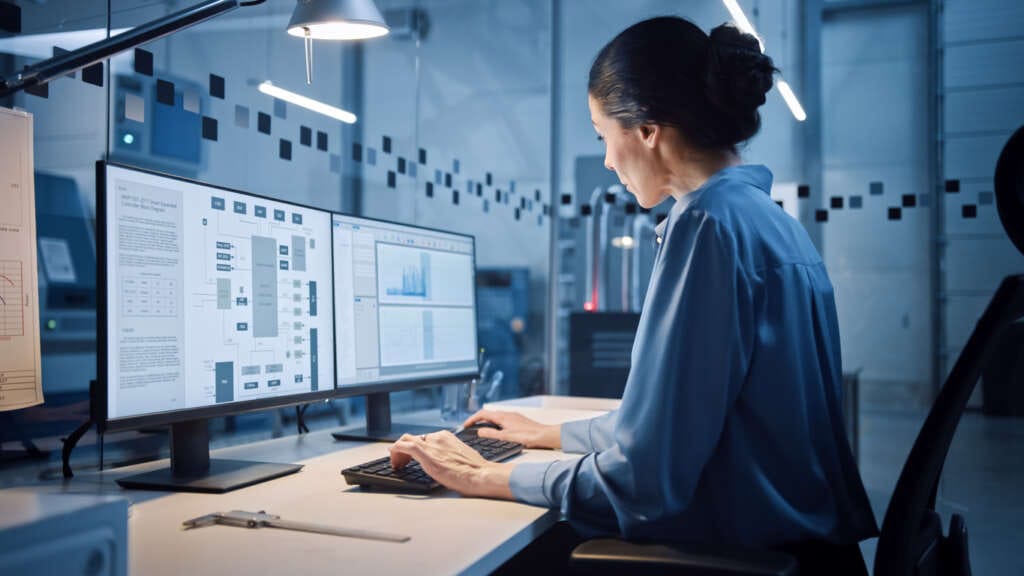
Smaller Manufacturers Must Leverage Their Unused Technology
Amanda Honig, Small, and Medium-Sized Business Industry Lead, Zebra Technologies
Manufacturers face some unique challenges in Europe right now. Stephen Phipson, CEO of Make UK, the manufacturing trade organization, said the sector counts 95,000 vacancies, equating to around £7 billion in lost output.
UK Government research says there are 53,000 fewer payrolled employees in the manufacturing sector compared to pre-pandemic levels. However, UK manufacturers plan to grow their businesses and create more jobs in the next five years. In Germany, 45% of manufacturers say they’re struggling to find properly trained staff, with manufacturing output declining in Germany and France due to supply chain pressure and price surges.
Across Europe, the knock-on effects of the pandemic, the ‘great resignation’, and rising energy, material, and transportation costs and shortages are hitting manufacturers. It’s why incentives to hold onto current employees and hire new people has become more of a priority for businesses, whether enterprise or small and mid-sized manufacturers.
SMBs Can Move Faster
Did you know small and mid-sized businesses (SMBs) can increase the output of their workforces more quickly than larger competitors? SMBs don’t have to worry about as much red tape as larger companies when it comes to implementing changes. Those that lean on technology to augment their workforce can help the few workers left on the floor carry the workload of a full team without feeling overwhelmed. Pickers can move twice as fast through pick lists when they know exactly where to go and the more efficient route to get there. Combining augmented reality or voice-picking guidance with a wearable mobile computer can help them fly through tasks frustration-free.
And forklift operators responsible for the movement of both raw materials and finished goods would certainly appreciate someone – or something – steering them in the right direction. A large-screen vehicle computer or tablet with voice navigation, perhaps? All they have to do is follow instructions.
The same is true of those working at the loading dock, where truckers have been reporting noticeable slowdowns as of late. If workers call out sick, you must be able to shift employees from one department to the next without it becoming disruptive. Even on a good day, such as a fully staffed day, many employees are filling multiple roles.
They can’t be expected to remember every process or anticipate when they need to be in a different department. At the same time, they shouldn’t be standing around at the loading dock waiting for trucks to arrive. Giving them mobile computers with software that can alert them when they’re needed at the loading dock to help with inbound or outbound loads is so simple, yet so impactful. Of course, those same mobile computers and wearables can then be used to guide them through the loading or unloading process.
The more direction your workers are given the better, as they won’t waste a minute trying to track down someone who can tell them what to do next. At the same time, they won’t be in a position where they must guess what to do or how to do it. They will be fully in the know at all times, and you’ll find you have better operational control as an organization, even when things are chaotic.
Even assembly line, quality inspection, and sourcing teams could benefit from some real-time guidance and automated decisions. In other words, the more “information” workers you have, the more your company’s size becomes irrelevant.
Fish or Fishing Rod?
Giving workers new technology and expecting them to know how to use it is like expecting someone to know how to use a brand-new electronic coffee maker without reading the instructions, just because they have used an electronic coffee machine before. Technology will only be beneficial if workers know how to properly use it.
I’m not just talking about powering on and off, logging in and out, or recharging, either. They need to know the purpose of every app, button, and feature, even if they don’t need it right away. Of course, the goal should be to give them technology tools that are so simple there are only a few buttons, apps, and features they’ll need to learn. As they saying goes: give someone a fish and they’ll eat for a day. Teach them to fish and they’ll eat for a lifetime.
Don’t assume that because they have worked in a manufacturing plant before that they know how to use mobile computers, printers, barcode scanners or radio frequency identification (RFID) readers or rugged Android devices.
Are You Sitting on an Untapped Technology Goldmine?
The priority is getting products out the door, so the time needed to update technology feels tight, even if better technology will help solve your challenges, better meet customer expectations, and allow you to pitch for contracts typically reserved for larger manufacturers.
You may be trying to make do with an outdated operating system or software platform, or hardware that’s missing a few key features that would make workers’ jobs easier.
Then again, many companies don’t realize workers already have the tools they need to be more efficient until they start looking at their current technology platforms from a different perspective. Are workers using all the apps and features available to them?
Could you quickly turn their devices into walkie talkies by adding push-to-talk or VOIP software? Or transform a handheld mobile computer into a voice-activated wearable to free up workers’ hands when they’re picking, packing, loading or unloading? Could your information systems be better integrated to ensure operations managers, workers and suppliers are making decisions based on the big picture?
Most likely, you will answer “yes” to at least one of those questions when you take a closer look at what you have already purchased as part of past technology implementations and upgrades. Just think about how many unused apps you have on your personal devices or how many features you don’t use on a regular basis – or ever – in your software platforms.
If you only have three workers to make, pack or inspect 100 orders a day, that’s okay. If those workers have the information and instructions needed to be super-efficient, your customers won’t know the difference. They’ll just know they got their orders on time, and the quality was superb. And, in this day in age, on-time delivery of complete orders is really all that anyone cares about.